News
Difference Between SMAW & GMAW Welding
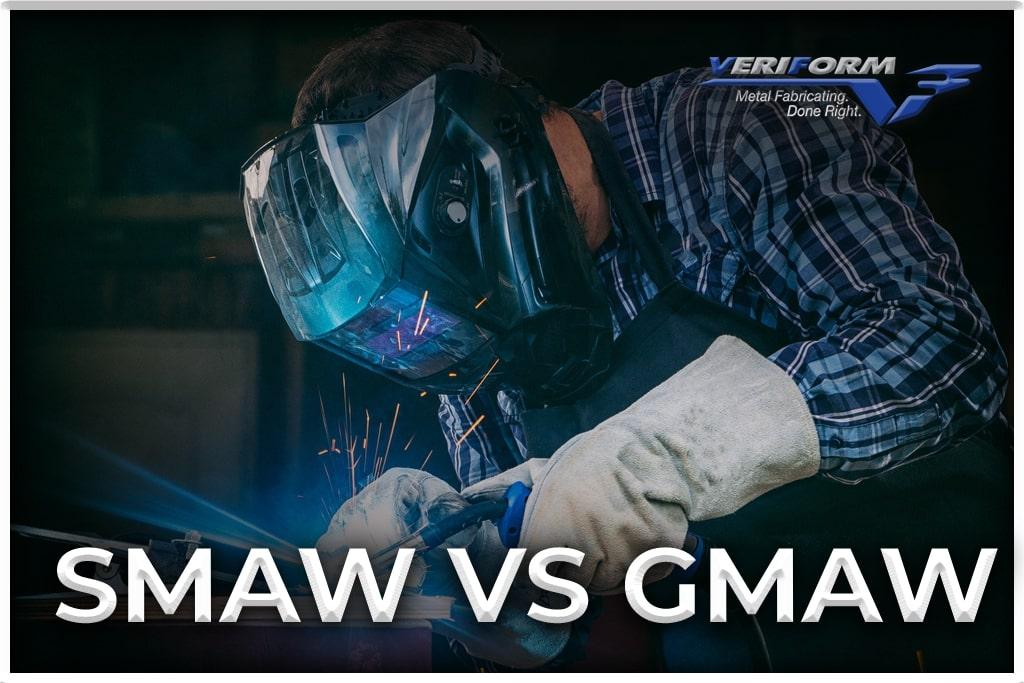
Shielded metal arc welding and gas metal arc welding (SMAW and GMAW for short) are two of the most commonly used welding techniques. However, those outside the industry don’t always understand the difference between SMAW and GMAW, making it difficult for them to select the right process for their metalworking project. In this blog, we explain how each option works, the differences between them, and when you might want to choose one over the other.
What is SMAW Welding?
Shielded metal arc welding (SMAW) uses stick electrodes with a flux coating on their surfaces. The process is used to weld ferrous metals like alloy steel, carbon steel, stainless steel, and cast iron. SMAW is typically used in fabrication work, although it can be applied in tasks like maintenance and repair.
After an electrode is placed in the holder, the electric supply is activated. Immediately after tapping the electrode on the metal workpiece, it is immediately withdrawn. The result is an electric arc with a high temperature that melts both the electrode and the workpiece.
During welding, the electrode transfers metal beads onto the workpiece, forming a weld pool. As flux melts, a shielding gas is released, covering the weld pool and preventing contamination. It is necessary to stop the process periodically to replace the electrode. The slag layer is chipped off after the weld pool solidifies.
What is GMAW Welding?
During gas metal arc welding (GMAW), a wire electrode is used, and no flux is added. GMAW welding, which can be used for alloys and metals like aluminum and stainless steel, is usually applied in metal fabrication and automotive processes. It’s also frequently seen in tasks involving brazing work and pipework.
The GMAW welding process is relatively straightforward. Once the shielding gas pressure and wire feed rate are selected, the DC supply is turned on and the electric arc is set up by tapping the electrode wire and withdrawing it. During the transfer of metal from the electrode to the weld pool, the shielding gas (usually argon, carbon dioxide, or helium) is ejected on the metal by the welding gun. Shielding gases are chemically inert, meaning that they do not interact with the weld pool. For this reason, GMAW is also known as metal inert gas welding, or MIG welding.
There are four types of GMAW welding:
- Short Circuit: An arc occurs between the consumable electrode wire and the base material, resulting in a short.
- Globular Transfer: The Globular method generates a large volume of weld metal that drips into the joint, as the wire is heated longer.
- Spray Arc: Weld joints are sprayed with small droplets of molten metal from the consumable electrode.
- Pulsed MIG: Pulse MIG welding produces one droplet of molten metal at the end of the consumable wire and the current, which pushes it across the arc and into the weld puddle.
What is the Difference Between SMAW and GMAW?
There are several important differences between the two processes.
- With GMAW welding, electrode changes are unnecessary because a wire feeder keeps supplying the gun with the electrode wire. This difference makes it more efficient than SMAW.
- An SMAW electrode has an external flux covering (one reason why it is known as stick welding), whereas a GMAW electrode has an external shielding gas.
- Due to its ability to lay down cleaner welds, GMAW promotes better efficiency. SMAW can leave slag deposits on the weld surface due to the vapourizing flux. The slag must be painstakingly removed once the weld has hardened, increasing the overall project duration. With GMAW, welds require less secondary cleaning.
VeriForm Inc.: Steel Fabricators You Can Trust
When you work with the steel fabrication team at VeriForm, you can be confident that whatever process is used (SMAW or GMAW), the welds will hold up to their intended applications. To ensure all specifications are met, we employ only CWB CSA W47.1 and W59 certified welders and retain a qualified CWB certified welding engineer. CWB-certified welding supervisors will also oversee your project from start to finish. To learn more, please visit our website, call 519-653-6000 or contact us online.