News
What is The Best Gas for MIG Welding?
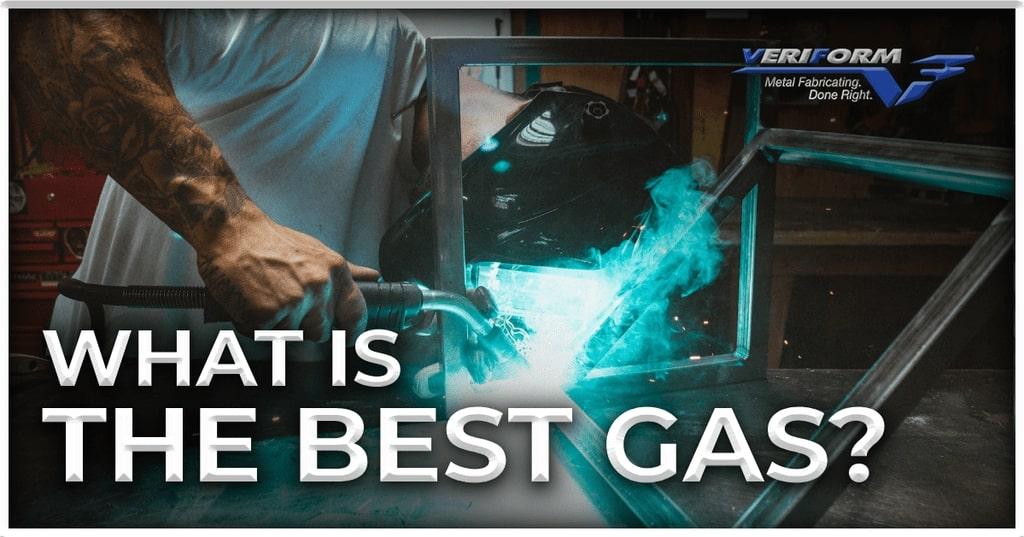
MIG welding is an arc welding process that uses consumable electrode wire along with gas that comes out of a nozzle that is connected to gas cylinders that contain different types of gases based on which metal is welded from here we take a deep dive into the types of gases used.
Types Of Gases that Could be Used in MIG Welding
There are two types of gases that are used for MIG welding. These are Inert gases (Argon & Helium) and reactive gases (Carbon Dioxide & Oxygen). Inert gases are used for their stability as they have a very low chemical reactivity with their surroundings. This allows them to work as a shield to protect the welding process. On the other side, reactive gases are highly active and chemically react with the weld pool which can cause a change in the properties of the metal in the welding process.
This also leads us to an important question of why gas is used in the welding process. The answer to this question is in the following points:
- Shielding
- Purging
- Blanketing
- Heating
Using Inert Gases Only for MIG Welding
As mentioned earlier, Argon has very low chemical reactivity. Using it alone for the welding process has its pros & cons.
Advantages of Using Argon in MIG Welding
- Handles long arcs at low voltages.
- Great results with non-ferrous metals like aluminum, copper, titanium, etc…
Disadvantages of Using Argon in MIG Welding
- The filler remains on top causing a tall bead.
- The outer edges of the arc remain cold, reducing penetration.
Moreover, helium is not often used alone but rather mixed with argon to benefit from both gas properties. For example, helium burns hotter allowing the penetration of the welding to become deeper welds.
Using Reactive Gases Only for MIG Welding
In MIG welding Carbon Dioxide (CO2) is the most commonly used reactive gas. It is the only reactive gas that can be used alone without mixing it with any inert gas.
Advantages of using only CO2 in MIG welding
- It’s the cheapest option out of the shielding gases. This makes it an attractive choice when low material costs are your main priority.
- Using only CO2 results in very deep weld penetration, which is useful for welding thick material.
Disadvantages of using only CO2 in MIG welding
- It has a less stable arc and more spatter is produced than when it is mixed with other gases.
- The short circuit process is the only welding option if your using CO2 gas.
Oxygen Is another reactive gas that is mixed with either inert gas like argon or with reactive gas like CO2 but adding a very small proportion of oxygen to any of these gases can change the result of welding dramatically.
Mixing Inert & Reactive Gases for MIG Welding
When welding, it is important that the welder uses proper mixing techniques for the inert and reactive gases. Two different types of gases are used in MIG welding which needs a design process for creating the optimal MIG welding mixture. To do so it is important to consider the cost, availability, and source of each gas. For example, if high-purity helium is not available, lower-purity gases can be used with minimal negative effects on weld quality and fusibility.
In addition to chemical properties, physical characteristics such as temperature, pressure, and composition must also be considered when planning a MIG Welding mix formula. the below table shows some of the mixing techniques used.
Metal | Thickness of Material | Shielding Gas |
Carbon Steel | 5/16 in. (8 mm) – 3/8 in. (10 mm) 3/32 in. (3 mm) – 5/8 in. (15 mm) 3/32 in. (3 mm) – 5/8 in. (15 mm) Above 3/8 in. (10 mm) | 95% Ar + 5% CO2 92% Ar + 8% CO2 90% Ar + 10% CO2 80% Ar + 20% CO2 / 75% Ar + 25 % CO2 |
Aluminum | Up to 3/8 in. (10 mm) OIver 3/8 in. (10 mm) | 100% Ar Ar +25%, 50%, or 75% He (Based on temperature) |
Stainless Steel | 1/25 in. (1 mm) – 1/4 in. (6 mm) 1/16 in. (2 mm) – 1/4 in. (6 mm) 1/16 in. (2 mm) – 1/4 in. (6 mm) | Ar + <35% He + <3% Co2 98% Ar +2% O2 10% Ar + 85%-90% He + 2-5% CO2 |
Best Practices for Choosing the Right Gas for your Welding Project
It’s important to pick a gas or gas mixture that matches the material being welded since some materials need certain types of gasses to properly weld. However, it also depends on cost and availability. For example, the most common gas used for MIG welding is argon because it has less carbon than other gases & doesn’t produce harmful gases to the environment. On the other hand, argon is much more expensive or penetrating compared to CO2.
For the best results consider the following:
- The penetration of the gas used.
- Arc Stability.
- Precautions for every gas & suitability for your welding environment.
- The availability of the gases used. For example, helium gas is not always available everywhere so replacing it with other gases might be the better option for a given situation.
- Cost of the gases. Argon & helium are not cheap while CO2 is very cheap compared to the other two inert gases.
Lastly setting the quality of the weld you want will make the decision much easier & precise in choosing the right gas or gas mixture.