News
Wielding Power: The Evolution and Advantages of Shielded Metal Arc Welding
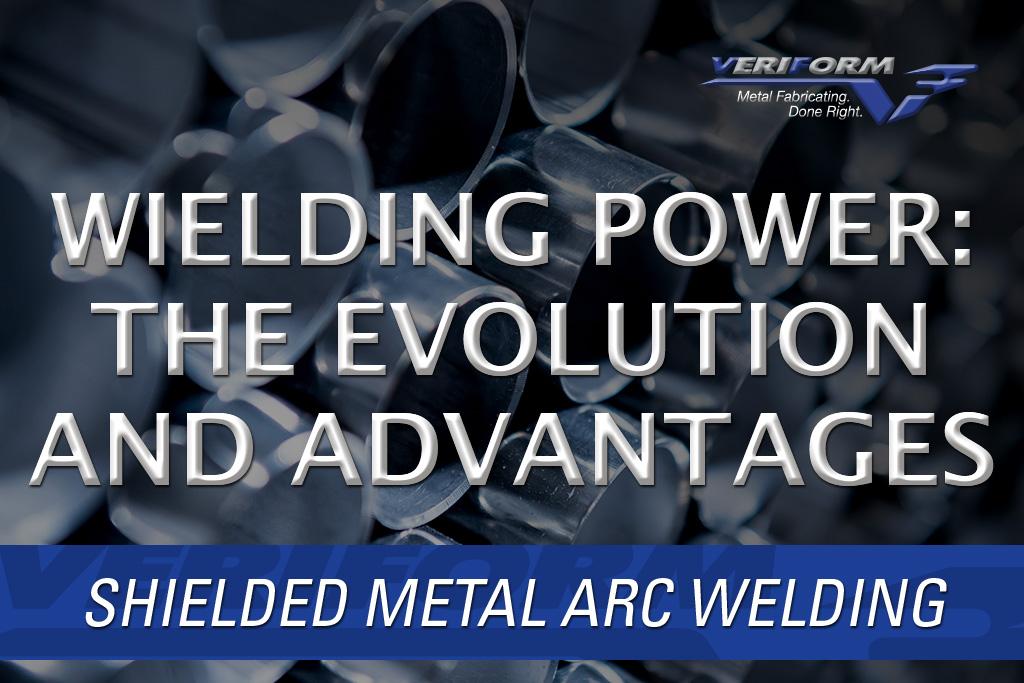
Shielded Metal Arc Welding (SMAW), also known as stick welding, is one of the industry’s oldest and most versatile welding processes. With a history of over a century, SMAW has evolved into a widely used technique for joining metals across various industries, from construction to automotive manufacturing. This article delves into the evolution, principles, and advantages of shielded metal arc welding, exploring its enduring relevance in the modern welding landscape and its role in shaping today’s infrastructure.
Evolution of Shielded Metal Arc Welding
Shielded Metal Arc Welding traces its origins to the late 19th century, with the invention of coated electrodes by Nikolay Benardos and Stanisław Olszewski in 1885. These electrodes, coated with a flux material, allowed for the creation of an arc between the electrode and the workpiece, producing a weld seam. Early applications of SMAW were primarily focused on joining steel structures in the construction and shipbuilding industries.
Technological Advancements
Over the years, shielded metal arc welding has undergone significant technological advancements, improving efficiency, quality, and versatility. Innovations such as the development of different electrode coatings, advances in welding power sources, and improvements in electrode composition have enhanced the performance and capabilities of SMAW. These advancements have expanded the range of materials that can be welded using the SMAW process, from carbon steel to stainless steel, aluminum, and beyond.
Principles of Shielded Metal Arc Welding
How Does Arc Welding Work?
Shielded Metal Arc Welding creates an electrical arc between a consumable electrode and the workpiece, generating intense heat that melts the base metals and the electrode, forming a molten pool. The flux coating on the electrode serves multiple purposes: it stabilizes the arc, protects the molten weld pool from atmospheric contamination, and forms a slag layer that helps to cool and solidify the weld. As the weld progresses, the electrode is consumed, and the slag can be removed to reveal the completed weld.
Components of a Shielded Metal Arc Welding Setup
A typical shielded metal arc welding setup consists of several components: a power source, welding cables, electrode holder, and welding electrodes. The power source provides the electrical current necessary to create the welding arc, while the welding cables transmit the current from the power source to the electrode holder. The electrode holder, or stinger, holds the welding electrode and allows the welder to manipulate it during welding. It is coated with flux material; the welding electrodes are the filler metal and flux source during welding.
Advantages of Shielded Metal Arc Welding
Versatility and Portability
One of the key advantages of shielded metal arc welding is its versatility and portability. SMAW can be performed in various positions, including flat, horizontal, vertical, and overhead, making it suitable for various welding applications. Additionally, SMAW equipment is relatively compact and lightweight, allowing easy transportation and setup in remote or confined work environments.
Cost-Effectiveness
Shielded Metal Arc Welding is a cost-effective welding process, requiring minimal equipment and setup compared to other welding methods. The simplicity of SMAW equipment and the availability of a wide range of electrodes at affordable prices make it an attractive option for small-scale welding projects and repairs. Additionally, SMAW electrodes have a long shelf life and do not require special storage conditions, reducing operating costs.
Applications of Shielded Metal Arc Welding
Construction and Fabrication
Shielded Metal Arc Welding is extensively used in the construction and fabrication industries, where it is employed to join structural steel components, plates, and pipes. SMAW is particularly well-suited for field welding applications, such as erecting steel structures, bridges, and pipelines, where access to power sources may be limited. Its versatility and portability make it a preferred choice for welding in outdoor or remote locations.
Automotive and Manufacturing
In the automotive and manufacturing sectors, shielded metal arc welding is used for various applications, including fabricating metal frames, chassis, and components. SMAW is well-suited for welding thicker materials and can produce strong, durable welds in high-stress areas. Its ability to weld various metals and alloys makes it a versatile solution for automotive repair and fabrication shops.
Conclusion
Shielded Metal Arc Welding, with its long history and enduring relevance, remains a cornerstone of the welding industry. From its humble origins to its continued evolution through technological advancements, SMAW has proven to be a versatile, cost-effective, and reliable welding process. Its ability to produce high-quality welds in various materials and environments makes it a preferred choice for various welding applications, from construction and fabrication to automotive manufacturing.
FAQs
What are the advantages of shielded metal arc welding?
Shielded metal arc welding offers several advantages, including versatility, portability, cost-effectiveness, and suitability for various welding applications. Its simplicity, reliability, and ability to produce high-quality welds make it a preferred choice for many welders and industries.
How does shielded metal arc welding differ from other welding processes?
Shielded metal arc welding differs from other welding processes using a consumable electrode coated with flux material. Unlike gas metal arc welding or gas tungsten arc welding, SMAW does not require an external shielding gas, making it suitable for outdoor and remote welding applications.
What are some arc welding examples?
Shielded metal arc welding is commonly used in construction, fabrication, automotive manufacturing, shipbuilding, and pipeline construction. It joins structural steel, plates, pipes, and other metal components in various industries and applications.
Is shielded metal arc welding safe to use?
The metal arc welding process is safe when performed correctly and with proper safety precautions. However, welders must be trained in proper welding techniques and safety procedures to minimize the risk of accidents, injuries, and exposure to hazardous fumes and materials.
How has shielded metal arc welding evolved?
Shielded metal arc welding has evolved significantly since its inception, with technological advancements leading to improvements in electrode coatings, welding equipment, and welding techniques. These advancements have expanded the capabilities and applications of SMAW, making it a versatile and widely used welding process.
What are some key components of a shielded metal arc welding setup?
A shielded metal arc welding setup typically includes a power source, welding cables, an electrode holder, and welding electrodes. The power source provides the electrical current necessary to create the welding arc, while the welding cables transmit the current to the electrode holder. The electrode holder holds the welding electrode and allows the welder to manipulate it during welding.
Tag