News
Welding Best Practices
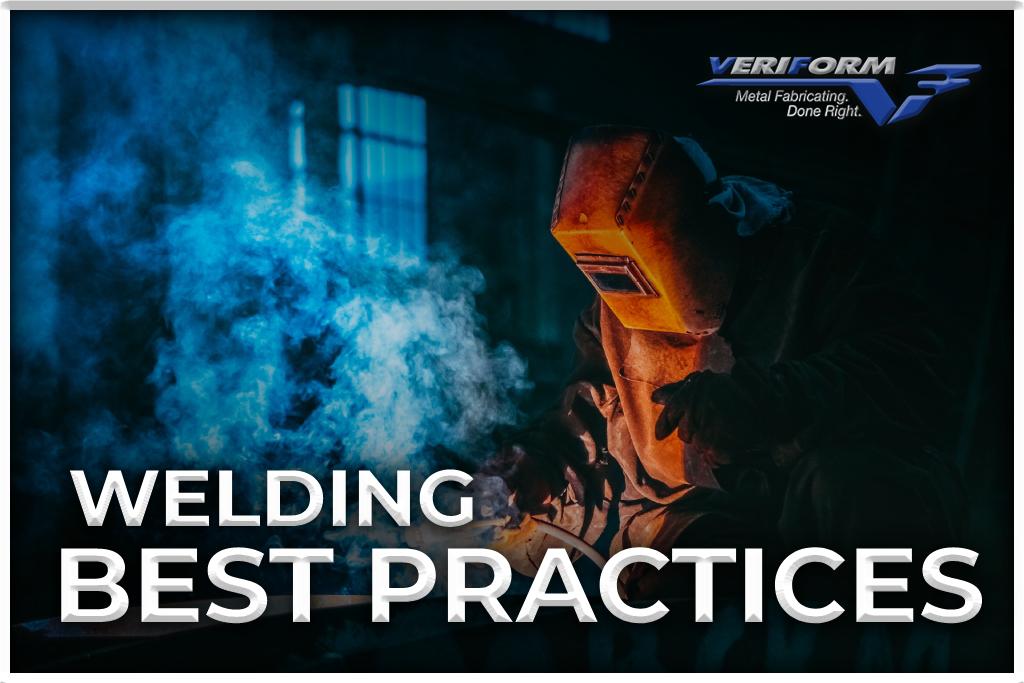
Welding is a process that consists of different technologies and an equally diverse range of materials. The process you use and the metal being worked on will largely dictate the tools and steps involved.
Having said that, there is a set of ‘golden rules’ that can be safely applied to all welding applications. In this article, the experienced fabricators at VeriForm Inc. go over welding best practices that will maintain both efficiency and the quality of your output.
Common Welding Challenges in Fabrication Environments
Although materials with a carbon steel base are often used in welding applications, they aren’t the only ones. Stainless steel, aluminum, and even bronze and titanium are becoming more common in manufacturing and fabricating environments. When you run an enterprise that welds different materials, you’re often looking at investing in more welding equipment as well as adjusting the schedule to accommodate equipment changeover between applications.
Do’s and Don’ts of Welding
Welding solutions designed for different types of materials can help you gain flexibility and efficiency while making high-quality welds. These best practices can help ensure you always have the right equipment on hand and use it to its best advantage.
DO Wear Appropriate Clothing and Safety Gear
Maintaining compliance with safety regulations and personal protective equipment (PPE) requirements is essential. This includes wearing the following during welding operations:
- A welding helmet to protect the worker’s face from sparks and the ultraviolet and infrared rays that the arc emits
- Clothing that doesn’t have pockets or cuffs that could potentially catch sparks
- Respiratory protection to keep the welding fumes at bay
DO Clean the Metal Surface
It’s important to properly prepare the metal before you weld it. This includes removing surface contaminants like dirt, paint, and rust and sanding away any cracks or uneven surfaces. In most cases, a simple going-over with a powered wire brush is sufficient, but be prepared to go further if needed.
Should it be impossible to clean an area before repairing it, don’t use an MIG welder on it. Instead, use a stick welder with a 6011 rod and go slowly so gas bubbles escape from molten welds before these impurities can be trapped.
DON’T Stick to Basic Feeders
Don’t limit yourself to basic options when selecting wire feeders. In welding operations where materials are frequently changed, wire feeders with more advanced technologies can save time and increase productivity.
Dual feeder systems eliminate the need for separate welding cells for different materials. Integrated systems that include the power source and feeder on a single MIG runner cart can save time during setup and make it easy to move the equipment from one cell to the next. Advanced wire feeders also allow welders to save different weld programs, making it easy to retrieve the correct parameters for specific applications.
DO Integrate Pulsed MIG Welding
Welders can produce high-quality welds and reduce rework by choosing a feeder and power source with pulsed MIG capabilities. Compared to CV MIG welding, pulsed welding is much better for aluminum because it provides lower heat input and greater arc control, reducing problems like burning, distortion, and spatter.
There are also advanced pulsed welding processes that help you produce a better-looking weld and bead profile: some versions even compensate for welder inexperience by supporting accurate travel speeds and correct distances between the contact tip and workpiece.
DO Incorporate User-Friendly Welding Technology
With materials like aluminum and stainless steel, it can be more difficult to set the correct welding parameters to support the desired bead profile and penetration. Consider welding technologies that make these parameters easier to attain. For example:
- There are welding power sources that assist welders in setting proper parameters. When the welder enters the material type, thickness, and wire size, the machine will establish the parameters necessary to create a quality weld.
- When welding aluminum, a power source with a crater and hot start provides better arc starting and stopping capabilities.
DO Choose the Right Filler Materials
It is critical to select the right filler metal for the application and base material. As aluminum and stainless steel come in many types, make sure the filler metal matches the base metal’s mechanical and chemical properties.
DON’T Use the Same Liner and Consumables for Different Materials
Welding steel should not be done with the same liner and consumables that weld aluminum. Cross-contamination or wire feeding issues can result. The liner for carbon steel is usually steel, while the liner for aluminum is plastic or Teflon with tighter tolerances. For the base material, you also need to use the correct feed guides and drive rolls.
DO Use the Appropriate Angle, Arc Spacing, and Speed
The correct angle will depend on the technology you are using. When wire welding, tilt the gun 10° to 15° in the direction you are pushing the weld. Maintain a 20° to 30° lead angle when stick welding.
When it comes to arc spacing, you’ll want to adjust your travel speed so that the arc remains within the leading third of the weld pool. With wire welding, maintain a distance of ⅜ to ½ inch. Stick welding requires a distance of 1/8” between the rod tip and the workpiece.
With travel speed, you’ll know that you’re going too slow when you’re producing convex, wide beads that have shallow penetration while depositing too much metal. If the travel speed is too high, the weld will produce a narrow, highly crowned bead. For most joints, the travel speed is well below 40” per minute.
VeriForm Inc.: Your Welding and Fabrication Experts
When you’re required to weld different materials, how well you adopt welding best practices can make a difference in your success rate. Pulsed MIG and advanced wire feeders allow operators to save time in setup and to produce high-quality welds, so investing in these additional capabilities can have a significant impact on the bottom line.
At VeriForm Inc., our CWB CSA W47.1 and W59 certified welders continually use welding best practices to ensure that we always meet your project specifications. We believe that in order to complete superior-quality welding, we need to use the best equipment and recommended technologies. To learn more about our metal fabrication services, please visit our website, call 519-653-6000 or contact us online.