News
Understanding Plasma Cutting: How Does It Work
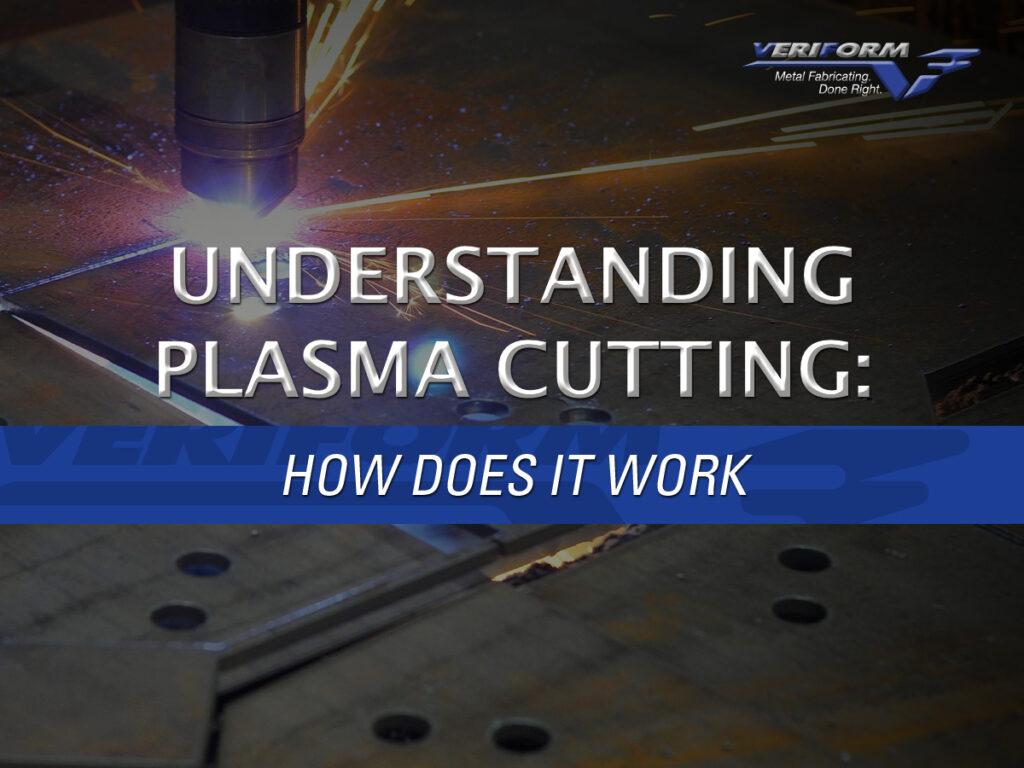
Plasma cutting is a versatile and efficient method used in various industries to cut metals of different thicknesses. This article explores the intricacies of plasma cutting, detailing its mechanics, applications, and advantages. By understanding how plasma cutters work and their role in modern manufacturing, one can grasp the significance of this technology in metal fabrication processes.
What is Plasma Cutting?
Plasma cutting is a thermal cutting process that uses a plasma arc to melt and sever metals. It is primarily used for cutting electrically conductive materials, such as steel, stainless steel, aluminum, copper, and other alloys. The process involves creating an electrically conductive plasma jet from an inert gas, typically compressed air, forced through a constricted opening. This plasma arc reaches up to 30,000°F (16,650°C), melting the metal and blowing away the molten material.
Components of a Plasma Cutting System
A plasma cutting system consists of several key components:
Power Supply
The power supply generates the electrical energy needed to create the plasma arc. It converts AC power to DC and controls the output voltage and current to maintain the plasma arc.
Plasma Torch
The plasma torch directs the plasma jet onto the workpiece. It includes a nozzle where the plasma arc is formed and an electrode that connects to the power supply.
Gas Supply
Compressed air or inert gases (such as nitrogen, argon, or hydrogen) create the plasma arc and blow away molten metal from the cutting area.
CNC Plasma Cutter Machine
Modern plasma cutting systems often include CNC (Computer Numerical Control) capabilities. A CNC plasma cutter machine uses computerized controls to precisely guide the plasma torch along a programmed cutting path, ensuring accuracy and repeatability in cutting operations.
How Do Plasma Cutters Work?
Plasma Arc Formation
1. Initiation: The process begins when a pilot arc is struck between the electrode (inside the torch) and the nozzle.
2. Ionization: The pilot arc ionizes the gas passing through the torch, turning it into plasma.
3. Plasma Jet: Once the plasma arc is established, the gas is forced through a small nozzle, constricting the arc and increasing its temperature to the point where it can melt metal.
Cutting Process
1. Material Preheating: The plasma arc preheats the material along the cutting path.
2. Material Melting: As the plasma arc moves along the metal, it melts the material along the cutting line.
3. Material Removal: Simultaneously, the force of the plasma gas blows the molten metal away from the cut, creating a clean and precise edge.
Applications of Plasma Cutting
Plasma cutting is widely used in various industries for its versatility and efficiency:
Metal Fabrication: Cutting metal sheets and plates for construction, automotive, and aerospace industries.
Industrial Manufacturing: Fabricating machinery parts, components, and structural elements.
Art and Design: Creating intricate metal artworks and sculptures.
Demolition and Salvage: Cutting and dismantling metal structures.
Pipe Cutting: Precision cutting of pipes and tubes for construction and pipeline industries.
Advantages of Plasma Cutting
Speed and Efficiency
Plasma cutting is faster than traditional methods like oxyfuel cutting, especially for materials of moderate thicknesses. It allows for high-speed cutting without compromising on accuracy.
Versatility
Plasma cutting can handle various electrically conductive materials and thicknesses, making it suitable for diverse applications across different industries.
Precision
CNC plasma cutting machines offer exceptional precision and repeatability, ensuring consistent quality in cut parts and reducing material wastage.
Cost-Effectiveness
With high cutting speeds and minimal setup times, plasma cutting is cost-effective for small-scale and large-scale production runs.
Minimal Heat Affected Zone (HAZ)
Compared to other thermal cutting methods, plasma cutting produces a relatively small heat-affected zone, minimizing distortion and preserving material properties.
Conclusion
Plasma-cutting technology has revolutionized metal fabrication processes with speed, precision, and versatility. Understanding how plasma cutters work—from the formation of the plasma arc to the cutting process—provides insight into its applications across various industries. As advancements continue, plasma cutting remains a cornerstone of modern manufacturing, meeting the demands for efficient, high-quality metal cutting solutions.
FAQs
What materials can be cut using plasma cutting?
Plasma cutting is primarily used for electrically conductive materials such as steel, stainless steel, aluminum, copper, brass, and other alloys.
How thick of a material can a plasma cutter cut?
Plasma cutters can cut a wide range of material thicknesses, from thin gauge metals (as thin as 0.5 mm) up to several inches thick, depending on the power of the plasma cutting system.
Are plasma cutters safe to use?
Plasma cutters are safe to use when operated correctly and with proper safety precautions. Operators must wear appropriate protective gear, including gloves, goggles, and flame-resistant clothing.
What are CNC plasma cutter machines, and how are they beneficial?
CNC plasma cutter machines have computerized controls that automate the cutting process based on programmed instructions. They offer precise cutting capabilities, high productivity, and the ability to replicate complex cutting patterns accurately.
Can plasma cutting be used for both straight cuts and complex shapes?
Yes, plasma cutting is versatile and can be used for straight cuts and intricate shapes. CNC plasma cutter machines can precisely follow complex cutting paths programmed via computer software.