News
Innovations in Metal Rolling Technology: Advancements and Future Trends
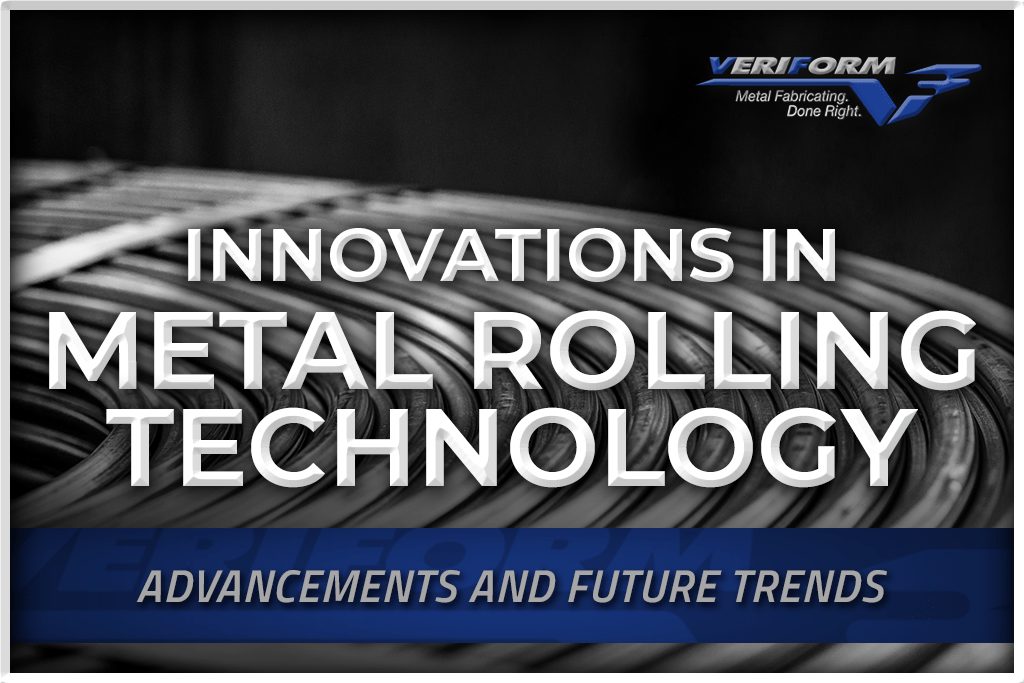
Metal rolling is a core materials processing technology that continues to advance through innovations. This article explores recent improvements in rolling mills, modeling software, safety features, and automation, shaping the future of metal rolling.
An Overview of Metal Rolling
Rolling reduces the thickness of metal stock and imparts desired mechanical properties through compressive forces. Hot metal sheet roll allows higher reductions versus cold rolling at room temperature. Rolling mill configurations like tandem, reversing, and ring mills employ massive rollers to shape metal into sheets, strips, and plates. The process accounts for over 90% of all metals produced today. Ongoing advances provide flatter, thinner, higher-quality rolls.
Smarter Control Systems and Instrumentation
Modern rolling mills are evolving into highly automated cyber-physical systems monitored and controlled by industrial computers and smart sensors. Refined gauge and shape measurement scanners feed into adaptive control models that adjust rolling forces in real time. Precision servo-electric motors replace hydraulic systems. Instrumentation upgrades support detecting and correcting deviations faster than human operators.
Advanced Simulation and Design Software
Software tools like finite element analysis and thermo-mechanical modeling better predict rolling forces, temperature effects, and product characteristics. Simulations assist engineers in designing optimal roll pass schedules and control strategies before physical commissioning. Virtual plant modeling helps visualize interactions between process variables. Next-generation rolling mills are configured by leveraging simulation for maximum efficiency and precision before operation.
Safer and Cleaner Mills
One focus of mill upgrades is improving workplace safety. Advanced fume extraction systems provide cleaner air quality. Sound-dampening materials and noise isolation reduce hearing hazards. Guarded pinch points, light curtains, and interlocks safeguard workers around machinery. Ergonomic handling equipment like manipulators and cranes reduces heavy lifting. Automation and remote monitoring further minimize direct exposure to hazards.
Novel Mill Configurations
Unique rolling mill designs continue to emerge optimized for specialized products. Inline mills with coordinated shears, slitters, and rollers enable single-pass production. Small- diameter roll cluster mills can handle geometries like tubes previously infeasible.
Continuous rolling processes boost throughput. Mills explicitly designed for challenging new alloys improve roll quality. Material-specific innovations target both productivity and final metal characteristics.
Smart Metal Transfer and Handling
Automated stock reels, conveyors, and coilers allow balanced material flow with zero downtime between mill stands. Intelligent transfer systems synchronize for continuous rolling.
Self-adjusting coilers and tension control adapt in real-time to ensure properly wound final rolls without overstretching. Precision material movement minimizes human involvement.
Power and Efficiency Improvements
Upgraded AC variable frequency motor drives provide better speed control and energy efficiency. Optimized lubrication flows reduce friction and waste. On-site heat capture and insulation conserve thermal energy. Proportional valves and pumps conserve hydraulic power. Many upgrades focus on reducing rolling power consumption while pursuing green manufacturing principles.
Leveraging Big Data Analytics
Refined sensors capture vast datasets on factors from product dimensions to equipment vibrations and temperature changes. Robust cloud-based analysis looks for correlations between variables and predicts deviations. By combining real-time data with historical patterns, rolling can be continuously refined through machine learning algorithms. Data-driven innovative mills will achieve levels of performance consistency that humans cannot match.
The Future of Intelligent Rolling
Looking ahead, the rolling mill will integrate even more comprehensive process controls, built-in defect detection, predictive maintenance alerts, and autonomous optimization. Combining metallurgical science with digitized systems will open new realms of efficiency and precision.
Rolling will move beyond an operational process into a strategic one where material characteristics are engineered at the molecular level. Technology innovations will shape the next generation of high-tech, low-emission, innovative rolling mills.
Conclusion
Rolling technology evolves rapidly through upgraded instrumentation, computational modeling, data-driven systems, and specialized mechanical designs. Integrating material physics with automated control networks will enable a new caliber of intelligent, precision rolling systems for producing the alloys and products driving 21st-century materials science and manufacturing.
FAQS
Q: How have computers changed metal rolling technology?
A: Advanced instrumentation, simulation software, predictive analytics, and adaptive controls allow more innovative monitoring and automation of variables like pressure and temperature during rolling. It enhances precision, consistency, and efficiency.
Q: What are the main types of rolling processes?
A: Common rolling processes include bar rolling for shaping steel bars, section rolling for vast flats and angles, steel rolling for thin gauge steel sheets, and toll rolling, where customized shapes are produced using specialized rollers.
Q: How does rolling impact metal properties?
Rolling enhances strength and hardness via strain hardening while improving uniformity in the grain structure. Careful control over temperature and reduction ratios lets engineers dial in desired characteristics.
Q: What is a sheet metal roller?
A: A sheet metal roller is a heavy cylindrical tool used in metalworking and sheet metal rolling processes. It reduces the thickness of sheet metal stock by compressing and forming the material as it passes through. Sets of rollers are used to achieve specific gauges.
Q: What is metalworking in Canada?
A: Metalworking Canada refers to various industrial processes that involve cutting, forming, and assembling metals. Many metal fabrication shops and metalworks across Canada perform metalworking activities like machining, welding, and finishing to produce parts for automotive, construction, manufacturing, and other sectors.