News
Can You Weld Carbon Steel?
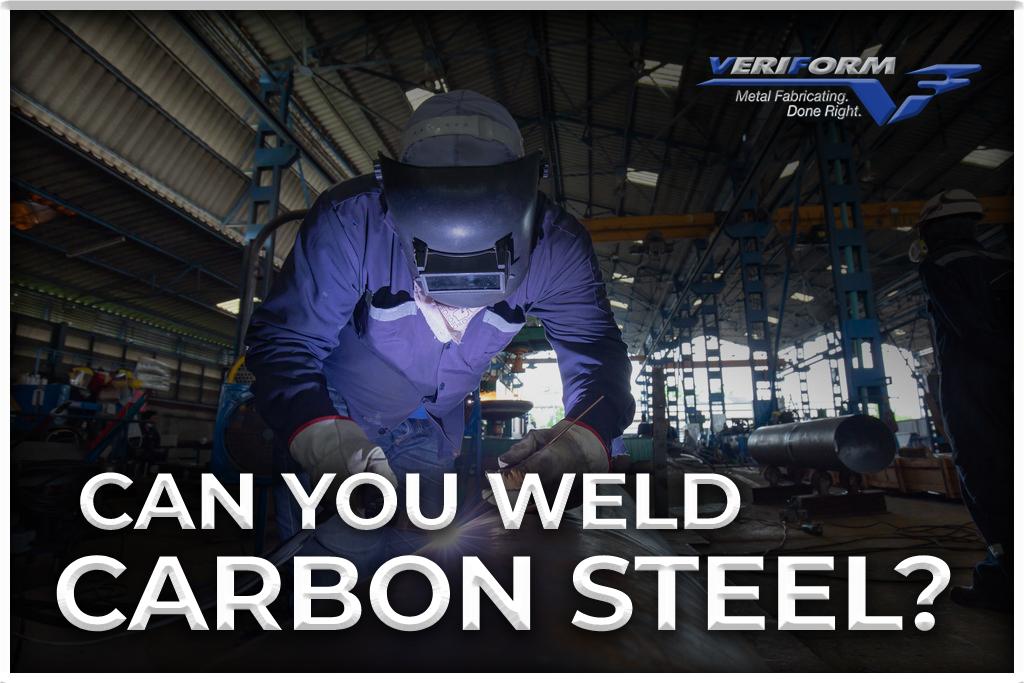
Carbon steel is an iron-carbon alloy with up to 2.1 wt.% carbon. Although carbon steels do not require minimum content of other alloying elements, manganese is often present. The copper, silicon, and manganese content should not surpass 0.6 wt.%, 0.6 wt.%, and 1.65 wt.% respectively. There are three types of carbon steel based on carbon content: low, medium, and high.
At VeriForm, Inc., we are often asked whether carbon steel can be welded. The answer is yes, but depending on the type, you may have to take certain approaches and precautions during the welding process. High carbon steel in particular is crack-sensitive and is prone to significant changes in its mechanical and physical properties after welding, so it is typically considered difficult to weld. However, even high-carbon steels can be welded without problems if you understand the characteristics that make different welding procedures necessary.
Considerations When Welding
Carbon steel is primarily composed of iron, but there are several other elements that can be added (carbon, for instance) that alter its weldability. When welding a project, it is crucial to understand what type of carbon steel is being used. Weld failure can result from ignorance of important variables, such as the added elements or carbon content range in each grade.
Welding carbon steel requires the following knowledge:
- Carbon Content: This content ranges from almost 0% by weight to around 2.1%, depending on whether it’s low, medium, or high carbon steel. Low-carbon steel like C1008 is typically the easiest steel to weld at room temperature. Preheating and post-heating are usually required for medium carbon steels such as C1045 while high carbon steel will most likely require more thorough preheating and post-heating processes to avoid cracking. A special welding filler metal may also be required.
- Carbon Equivalency: A carbon equivalency formula takes into account other elements in the steel that can affect weldability. The higher the carbon equivalent, the less weldable the carbon steel is. Carbon equivalencies are generally more of a concern with alloy steels.
- Cooling Rate: Choosing the right carbon steel to weld also depends on its weld cooling rate. Weld cracking can be exacerbated by high cooling rates. With carbon steels with higher carbon contents and other elements in the carbon equivalency formula, cooling rates should be slowed to prevent weld cracking. Weld cooling rates can be affected by the thickness of the steel as well as ambient temperature.
It is important to note that there are some elements in carbon steel that are not conducive to welding, no matter how much preheat or filler metal is used:
- The presence of lead may contribute to solidification cracking, so welding should not be performed on leaded steels.
- Sulphur and phosphorus can also cause weld cracking. Carbon steel with a small amount of sulphur or phosphorus can be readily welded; however, steel with more than 0.05% of either could develop solidification cracks. A high level of sulphur and phosphorus makes free machining steels like C1141 unsuitable for welding.
Can You Weld Carbon Steel to Steel?
For many applications, stainless steel is an excellent choice. However, it can be expensive when you want to fabricate large workpieces. A lower-cost carbon steel can therefore be used for non-essential parts and frameworks in larger fabrication projects to help reduce costs.
A strong bond between carbon steel and stainless steel requires special attention to details like heat, filler material, and joint design. Joint preparation, root openings, and preheating are crucial, as are maximum interpass temperatures. In addition:
- Stainless steel requires close monitoring of heat input. It is necessary to control the heat and limit the time in the sensitization temperature range. In areas affected by too much heat, corrosion resistance will be reduced.
- Different filler metals are required when welding dissimilar metals. In order to prevent an unsatisfactory alloy from forming, stainless electrodes with higher alloy content are used.
For these types of projects, you want to ensure that you work with a skilled and reputable Ontario steel manufacturer.
Which Welding Method is Best for Carbon Steel?
Low and medium-carbon steel is typically the easiest metal to weld. There are different techniques you can choose from.
Arc Welding
One of the most common welding methods for low-carbon steels is an arc or stick welding. During arc welding, a high current passes through a pair of cables attached to the machine’s live and earth terminals. A flux-covered electrode is clamped into a spring-loaded clamp on the live cable. Another clamp secures the earth cable to metal workpieces. Intense heat is produced when the electrode is brought close to the metal. The heat melts metal at the weld point, and the resulting melted flux pool prevents contamination of the weld through oxidation.
Gas Metal Arc Welding
Gas metal arc welding, or MIG, is another common carbon steel welding method. This process works similarly to arc welding, except that the electrode is a continuous wire strand that is fed into the welding point by the welding machine. Weld pools are shielded from contamination by a constant stream of argon gas or argon/helium mixture.
Gas Tungsten Arc Welding
Gas tungsten arc welding, or TIG, is less commonly used, but still a highly effective means of welding carbon steel. Because of its versatility, argon has become the most popular gas used for TIG welding carbon steel and non-alloy steel. It is easy to initiate the welding arc, making it ideal for all types of arc initiation systems.
VeriForm Inc.: Experienced Carbon Steel Fabricators
The versatility of carbon steel makes it suitable for a wide range of applications. VeriForm Inc. provides quality carbon steel parts on time using state-of-the-art equipment and decades of industry experience. Over the years, we have acquired a reputation for product excellence and short lead times.
Our team can assist you throughout the entire process, from the initial design phase to the fabrication of your custom carbon steel part to shipping your finished product, ready for installation. To learn more, please visit our website, call 519-653-6000 or contact us online.