News
What is SMAW? A Deep Dive into the World of Welding
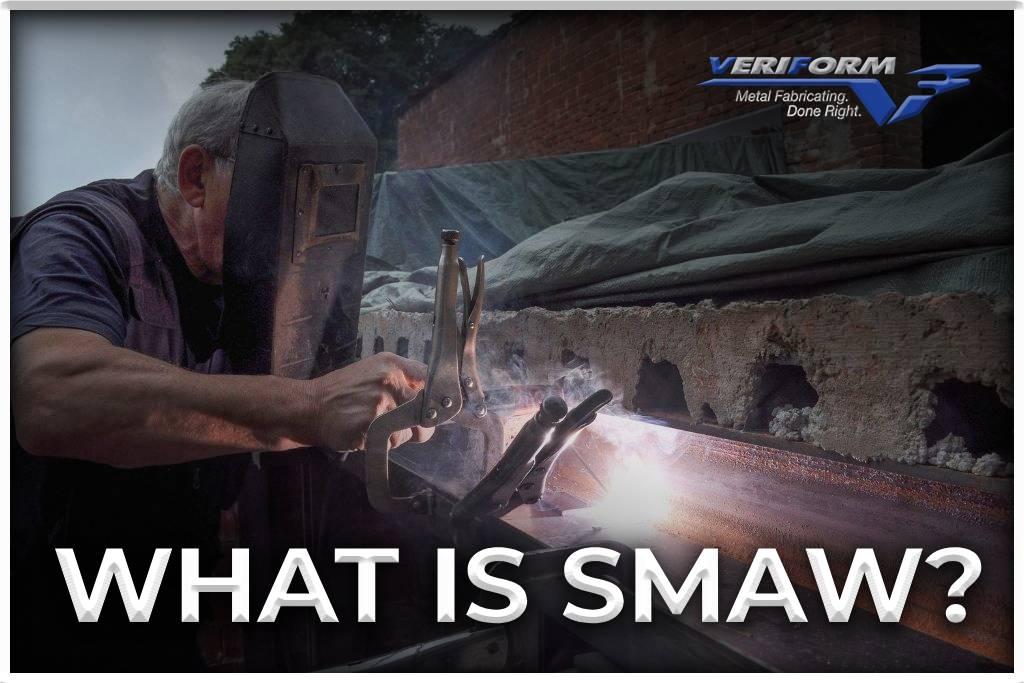
You’ve probably heard the term “SMAW” being thrown around in the world of construction and manufacturing. But what is SMAW? Let me break it down for you in the most engaging and storytelling way possible.
How Does SMAW Work?
Imagine you’re trying to join two pieces of metal. It’s not as simple as just sticking them together with some glue, right? This is where SMAW comes into play. SMAW, or Shielded Metal Arc Welding, is a method used to join two pieces of metal together using an electric current. The current creates an arc between the metal pieces and an electrode, causing them to melt and fuse together.
Picture this: It’s a summer day, and you’re trying to melt two ice cubes together. By placing them close and applying some heat (maybe from the sun), they’ll eventually melt and fuse. SMAW works similarly, but instead of ice, it’s metal, and instead of the sun, it’s an electric arc.
The Components Of A Stick Welder
Let’s dissect a stick welder, the primary tool for SMAW. Think of it as a magical wand that can join metals.
- Power Supply: This is the heart of the stick welder. It provides the necessary electric current.
- Electrode Holder: Have you ever seen those gripping tools? That’s this. It holds the electrode securely.
- Ground Clamp: This ensures that the circuit is complete. It’s typically clamped to the workpiece.
- Cables: These are the veins transferring the electric current.
Using a stick welder is akin to using a pen. But instead of ink, you have molten metal. And instead of paper, you have pieces of metal longing to be joined.
The Role Of The Electrode In SMAW Welding
We’ve talked about the stick welder, but what’s the role of the electrode? Imagine the electrode as a candle.
The outer coating, or the “flux,” protects the molten weld from contaminants in the air, like oxygen. As the electrode burns, it also provides filler material that aids in the joining of the metals. So, it’s like a two-in-one package: protection and filler!
Understanding The Welding Arc In SMAW
The arc is the unsung hero of SMAW. It’s the bridge between the electrode and the metals. When you strike an arc, you’re essentially creating a channel of electricity, producing heat upwards of 6,500°F. This heat melts the metal and the electrode, making fusion possible.
Imagine a rainbow, but instead of water droplets and sunlight creating a spectrum of colours, you have an electrode and electric current creating a blinding light and intense heat. That’s the welding arc for you!
In conclusion, when someone asks, “What is SMAW?” you can now regale them with tales of electric arcs, molten metal, and the magic of welding. It’s not just a technical process; it’s an art form and a science. So the next time you see a structure standing tall or a vehicle zooming past, remember the role SMAW might have played in bringing that piece of engineering to life.
Advantages And Disadvantages Of SMAW (Stick) Welding
Welding techniques are a dime a dozen, but SMAW, often referred to as Stick Welding, stands out for specific reasons. Like everything in life, it has its pros and cons. Let’s jump right into what makes it shine and where it might need a little polish.
Benefits Of SMAW
- Versatility: One of the significant advantages of SMAW is its versatility. You can weld a variety of metals and alloys, making it a go-to method for many welders.
- Portability: Unlike some bulky welding setups, SMAW equipment is relatively compact. This means you can easily transport it to various job sites.
- Cost-effective: Initially, the setup cost for SMAW is lower compared to other welding techniques. So, for beginners or those on a budget, it’s a viable option.
- Less Sensitivity to Wind and Drafts: While some methods get disrupted by environmental factors, SMAW is robust. This is especially crucial for outdoor welding tasks.
- Simple Equipment: The equipment used in SMAW is straightforward and user-friendly. There’s no need for a sophisticated setup or intricate machinery.
Limitations Of SMAW Welding
- Skill Dependency: SMAW requires a higher level of skill. Mastery takes time, and there’s a steep learning curve involved.
- Slower Welding Speeds: Compared to processes like MIG or TIG welding, SMAW is generally slower. This can affect productivity on larger projects.
- Frequent Electrode Changes: The electrodes used in SMAW aren’t very long. This means frequent stops and starts to replace them.
- Clean-up: The flux coating on the electrode can create slag, which requires chipping and brushing post-welding. This adds an additional step to the process.
- Not Ideal for Thin Materials: Due to the intense heat produced by SMAW, it might not be suitable for thinner materials, which could warp or burn through.
Conclusion
SMAW, or Stick Welding, is an age-old technique with admirers and critics. While it offers the benefits of versatility, cost-effectiveness, and resilience against environmental factors, it also poses challenges in terms of speed, skill requirement, and maintenance. Like any tool or method, its efficiency is often determined by the task at hand and the operator’s skill. Knowing when and where to use SMAW will ensure optimal results every time.
FAQs
SMAW stands for Shielded Metal Arc Welding. It’s a manual arc welding process that uses a consumable electrode covered with a flux to lay the weld.
SMAW primarily uses stick electrodes and is known for its simplicity and versatility. Unlike TIG or MIG welding, SMAW doesn’t require an external gas supply.
SMAW is versatile and can be used to weld a range of metals, including carbon steel, stainless steel, cast iron, and certain alloys.
It’s cost-effective, the equipment is straightforward, and the process is more tolerant to surface contaminants compared to other methods.
Yes, SMAW can be slower than other methods, requires frequent electrode changes, and the resultant slag needs post-welding cleanup.
Not always. While it’s great for thicker materials, the intense heat can cause issues like warping or burn-through on thinner metals.
No, one advantage of SMAW is its resilience to environmental factors, making it suitable for outdoor welding tasks.